How To Develop A Quality Management System
Estimated reading time: 5 minutes
Successful organizations understand the importance of managing organizational quality.
We can all provide an example of an experience with an organization with poor product or service quality.
The experience may have been an interaction with a rude employee at a store or a damaged product that was ordered online. Either example shows how committed the organization is to quality.
But before quality can be managed, it needs to be defined.
What is quality?
“The organizational structure, processes, procedures, and resources needed to implement, maintain, and continually improve quality management.”
American Society for Quality (ASQ)
Employees should understand how the organization defines quality and the importance of maintaining high-quality services and products.
They also need to know how what they do impacts products and services.
For instance, employees need to understand that products absent from defects and services that exceed customer expectations are the cornerstone of a quality organization.
This is done by creating internal systems to control product and service quality.
7 Steps to Developing a Quality Management System
1. Create A Written Document That Defines Quality
Quality is determined by how it is defined and measured.
Create a document articulating the organization’s commitment to quality products and services and its commitment to total quality management (TQM).
These policies provide specific details as to what falls under the scope of organizational quality, what it looks like, and how it is measured.
For instance, quality for a call center may be defined as an organizational expectation for superior customer service on the phone and measured by wait times, hold times, and abandoned call rates.
Another example might be a restaurant. In this example, quality might be measured by order-to-table times, customer feedback on food quality, or the number of meals returned.
This document should outline what quality looks like for every process, product, and service.
2. Develop Procedures
Employees work best when they have specific step-by-step procedures to follow.
The more complex the system, the more specific policies and procedures need to be. Develop procedures for the users of the system. These procedures should be specific enough to reduce the bureaucracy and red tape, speeding up the process.
Write procedures and answer the questions: who, what, where, and when.
For instance, a call center may have detailed procedures for how to answer the phone (phone script), how to diffuse an angry customer, or how to sell additional products to a customer.
Employees are trained to use these detailed procedures and are monitored for consistency in practice.
In the restaurant example, a waitress may have specific instructions for how to interact with customers (service standards), how to manage customer complaints, or how to engage with customers and upsell drinks or desserts.
3. Develop Work Instructions
Create work instructions for how the work should be done.
All jobs should have detailed job descriptions that articulate job expectations.
Use process maps to identify steps in the process and job aids to provide a visual for properly completing a job task.
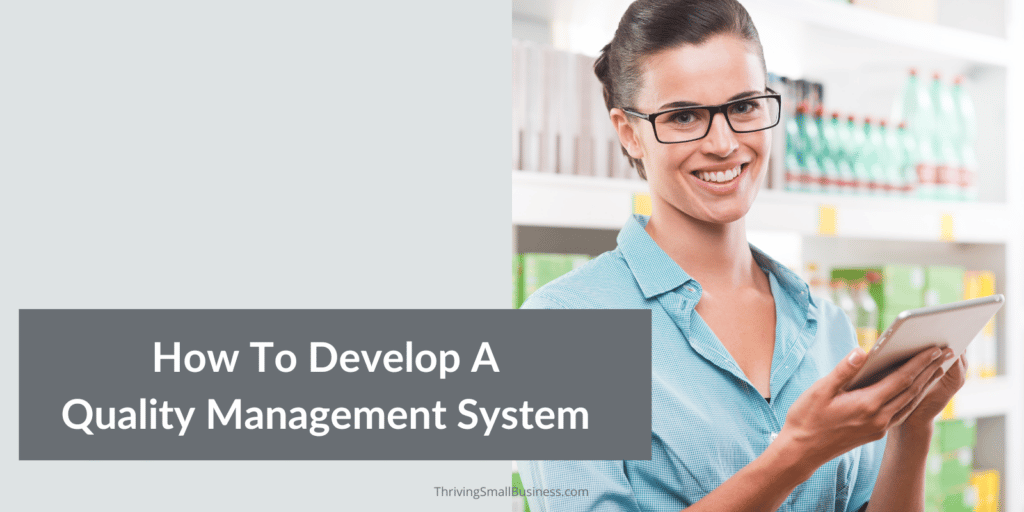
For instance, if the call center has a storage area, use printed signage to show where supplies are kept or laminated instructions for answering the telephone.
Take the time to provide these visual reminders to help employees maintain consistency in practice.
4. Collect Data
Create processes for collecting data to monitor if work is being done according to policies and procedures (evidence).
Once you determine what data you want to collect, create a process to collect, store, and report it.
Assign responsibility to one person to track, analyze, and report results.
For instance, a call center phone system should be able to provide a wealth of data that shows wait times, hold times, abandoned call rates, and recordings of employees interacting with customers.
Use this data to create improvement plans and training programs.
5. Quality Training
Help employees understand why quality is important by conducting ongoing training.
This training should be at a micro and a macro level.
Micro training will be at the local level. This is where employees learn the exact steps to perform their job assignments. Include service standards and specific job details.
For instance, a waitress might learn how your restaurant would like for them to interact with customers. This includes greeting them, introducing themselves, tending to their needs, etc.
At a macro level, employees would learn about the mission and vision of the organization. This high-level understanding helps employees see the purpose of what they do.
Share the quality data that you collect. This might include measurable data such as call wait times or customer feedback comments.
Use this data to help employees see the big picture and how what they do really does impact the customer experience.
6. Reward and Recognize Good Performance
Provide incentives for employees to provide quality products and services.
Create programs that are specifically designed to acknowledge consistent quality work and great customer service.
For example, gather employees at a monthly meeting or annual event designed to recognize those employees who exemplify quality for your organization. Create an employee of the month or year award and offer a prize that employees yearn for.
I used to work for an organization that had an Employee of the Year award. This person was given a paid week off of work and a trip for two to any number of destinations.
This incentive made most employees aware and worked hard for this coveted prize.
7. Weed Out Employees Who Don’t Get It
There will be times when you have employees who do the bare minimum and simply don’t care.
These underachieving employees not only have a negative impact on customers but also create resentment among those employees who are working hard and trying to do the best they can.
Find a way to identify and transition these employees onto a new job.
As Jim Collins so famously said in his book Good-to-Great, “have the right people on the bus and the right people in the key seats before they figure out where to drive the bus.”
Don’t allow the wrong employees to affect your quality efforts and how customers perceive your products and services.
Quality Organizations Have A Competetive Advantage
Organizations that can manage the quality of their products and services have an advantage over the competition.
This high-quality standard reduces or eliminates product defects and service blunders.
Take the time to evaluate your quality efforts and create a process to manage and control product and service quality. Your customers will be glad you did!