How to Develop a Safety Program in 6 Easy Steps
Estimated reading time: 5 minutes
According to the OSHA website, 5,333 workers were killed on the job in 2019. This staggering number represents more than 100 deaths a week or 15 deaths per day.
The Bureau of Labor Statistics also reports that another 2.8 million workers experienced nonfatal workplace injuries and illnesses in 2019.
“Making a living shouldn’t have to cost you your life. Workplace fatalities,
injuries, and illnesses are preventable. Safe jobs happen because employers
make the choice to fulfill their responsibilities and protect their workers. “
Dr. David Michaels Assistant Secretary of Labor for Occupational Safety and Health
These staggering numbers speak to an employer’s responsibility to provide a safe and hazard-free workplace.
Having a well-defined safety program can help keep a focus on maintaining a safe workplace.
The goal of a safety program should be to create a system to support the identification, evaluation, and prevention or control of hazards that go beyond legal requirements.
The system should also train employees to be aware of, and understand safety issues.
Use employees to help identify potentially dangerous work areas and things that need correcting. This involvement by your team helps make them aware and encourages them to take ownership of workplace safety.
As organizations grow and workplace complexities increase, the need for written guidelines, policies, and procedures increases.
Invest the time to articulate and put your policies in print or digital format so employees can use them as a reference.
However, written guidelines are not as important as the effectiveness of the safety program.
And, policies and procedures are only as effective as how they are enforced.
How to Develop a Safety Program
1. Appoint A Safety Officer
Someone should be given the responsibility to oversee the safety program. This ideal person should have an understanding of their responsibilities and accountability for maintaining a safe workplace.
A safety officer monitors workplace activities to ensure that workers comply with company policies and government safety regulations.
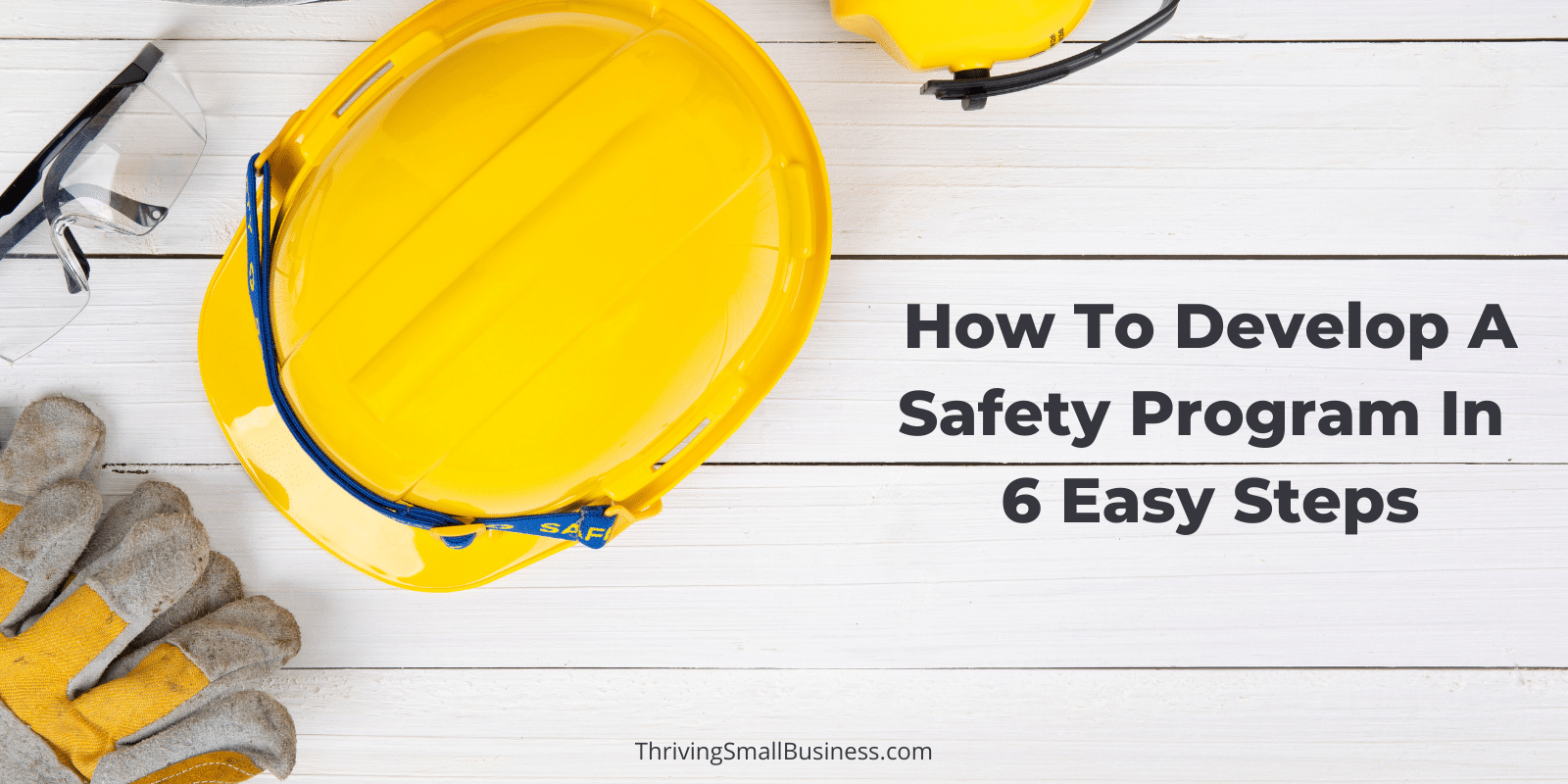
Some of the safety officers’ duties include policy development, safety inspections, safety training, and compliance with OSHA standards.
These responsibilities should be included in the employee’s job description and incorporated into the employee performance management process.
2. Perform A Safety Inspection
A workplace safety inspection should be done regularly to identify areas that need correcting.
A safety inspection will identify fire emergency exits, things that could cause a slip or fall, inspecting exits for clear routes, ensuring ergonomics are used properly, adequate lighting, protective clothing (where applicable), proper use of chemicals, and maintenance equipment safety issues.
This safety inspection process should also include a review of new facilities, materials, equipment, and all related processes.
3. Perform Safety Incident Investigations
It is important to conduct a safety investigation as soon as an incident is reported – ideally within 24 hours.
When investigating an incident, try to answer the who, what, where, when, how, and why of the incident.
Asking and answering these questions will allow you to drill down on the issue and make recommendations for a safety improvement plan.
An incident report should also be completed for every accident, injury, or illness that happens in the workplace.
Safety improvements should be documented and maintained in the safety officer’s office. OSHA has some reporting requirements that can be found on the OSHA Website.
4. Form A Safety Committee
Establish a safety committee to oversee the entire process.
The safety committee should include front-line employees, facility/maintenance representatives as well as other leaders in the organization.
Front-line employees can help identify and resolve health and safety problems because of their unique perspective.
Committee Responsibilities:
Identify Workplace Hazards
This should include inspections of all buildings and talk to workers about unsafe work practices and potentially hazardous conditions.
The safety committee is also responsible for writing policies and procedures for inspections.
Assess Safety Issues
This is done by reviewing accident records and looking for trends that might contribute to hazards.
There should be an accident investigation, and a review of recent incident reports and accidents should be done before every inspection.
An annual review of the safety program should also be done.
This is simply a time to review the safety policies and conducting a walk-through of the organization.
Problem Resolution
Management of safety involves following up on all issues and ensuring resolution has been made.
This is in addition to correcting issues and general oversight of the safety management of the organization.
Safety Records
The safety committee should keep records of all incidents, safety meetings, and any recommendations that are made.
5. Perform Safety Training
All employees should be required to go through safety training.
A class on workplace safety will help employees understand safety policies and procedures and their responsibility to maintain a safe work environment.
This training should include identifying unsafe work conditions, the process of reporting of illness or injury, and the use of personal protective equipment.
Employees who work with hazardous materials should be trained on proper handling, storage, and use of chemicals.
For instance, the custodial staff should be trained on the proper use and handling of cleaning products.
Training should also include new processes or procedures as they are introduced or new equipment that may pose a hazardous situation.
It is important that employees have a reporting process to alert management of potential hazards.
Lastly, this training should be documented and incorporated into the new employee orientation process.
6. Safety Must Have a Down Approach
Employees will only be as committed to workplace safety as senior leadership demonstrates.
Safety must have a top management approach that is communicated throughout the organization.
The more visible leadership is in supporting workplace safety, the more successful it will be.
According to the OSHA website, effective management of worker safety and health programs not only benefits workers but also helps the organization by:
- Reducing the extent and severity of work-related injuries and illnesses.
- Improving employee morale and productivity.
- Reducing workers’ compensation costs.
No one can argue that providing a safe workplace for your employees is simply the right thing to do.
But, maintaining a safe workplace can also benefit your organization by improving employee morale and reducing workers’ compensation costs.
For more information on how to improve the safety of your workplace visit the OSHA website.
When was the last time you assessed the safety of your organization?
You can learn more about workplace safety by reading Basics of Occupational Safety